Overview
Maintenance programs are designed to preserve and restore equipment reliability by replacing worn components before they actually fail.
Equipment OEMs provide factory-recommended maintenance schedules (planned maintenance schedules), which need to be followed to maintain warranties and to keep the equipment running as designed. They contain checklists of tasks that technicians need to perform at specific intervals over the life cycle of the asset.
Successful preventive maintenance programs help you avoid breakdowns of vehicles and equipment, ensure your assets are always running at peak performance, and extend their service lives.
Terminology
Schedules
A Maintenance Schedule is a collection of one or more Maintenance Plans.
Schedules are not required to track the maintenance of your fleet, but they can simplify collections of complex plans and allow you to visualize the entire maintenance life cycle of your assets.
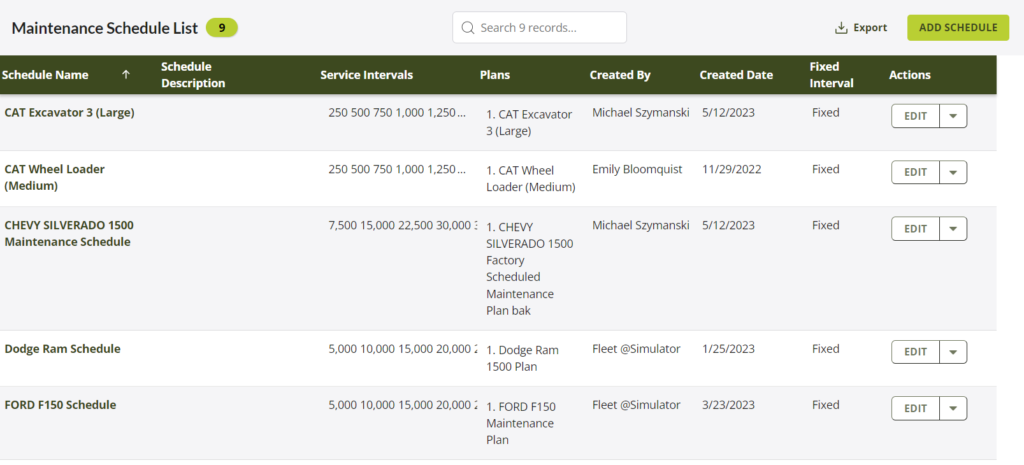
Plans
A plan is a collection of tasks, which can be assigned to any number of assets.
A plan consists of three main components:
- Service Intervals: When the plan will be repeated. Can be one-time or recurring.
- Tasks: A list of services for the asset.
- Assets: Plans can be applied to individual assets, groups, or the entire fleet.
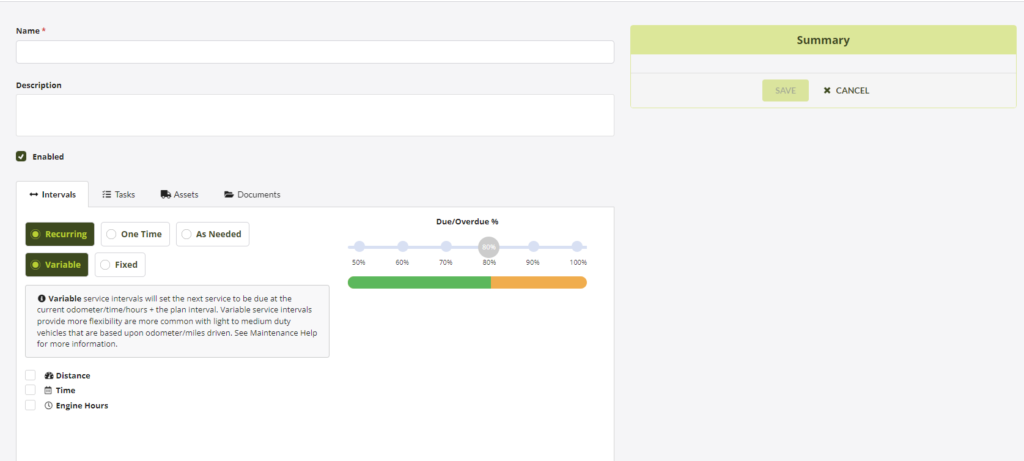
Tasks
Tasks are the smallest unit of work to be performed by the service technician. A Plan can contain many Tasks.
Example: “Oil Change Plan”
- Task: Change Oil
- Task: Replace Oil Filter
- Task: Check Air Filter
- Task: Check Tire Pressure
- Task: Top-off all Fluids
Service Intervals
A service interval is a set of conditions which determine when the maintenance plan repeats.
Service intervals can use any combination of:
- Distance travelled (via Odometer)
- Time (every # of days)
- Engine Hours
Intervals can be fixed or variable
- Fixed interval: service due at a specific
distance/time/engine hour
- For example, a service interval set for every 500 hours will be due at exactly 500/1,000/1,500/2,000/etc. hours. If maintenance is performed at 600 hours, it will be due again at exactly 1,000 hours (not 1,100 hours).
- Variable interval: service due at the plan
interval, starting from the current odometer/time/engine hours.
- For example, an oil change may be set for every 3,000 miles. However, if the vehicle is serviced at 4,000 miles, it will not be due again until 7,000 miles (not 6,000 miles).
Logs
Maintenance Logs are the service history of your assets. Service notes and maintenance costs can be added to a Log.
You can log unscheduled repairs or services, even if they are not associated with a Maintenance Plan.
Once a scheduled maintenance plan has been logged as complete, the next scheduled maintenance will be automatically generated.
Diagnostic Trouble Codes (DTC)
Diagnostic Trouble Codes (DTCs) are a vehicle’s self-diagnostic and reporting capabilities.
On-board diagnostic systems report the status of the various vehicle subsystems, and can communicate problems via DTC codes. DTC codes allow a technician to rapidly identify and remedy malfunctions within the vehicle.
The Temeda system supports both OBDII fault codes and J1939 DTC Information such as SPN, FMI, Occurrence Count and Conversion Method.
OBDII DTC example:
- Diagnostic Information:
- Fault Code: P0171
- Fault Location: System too lean, bank 1
- Probable Cause: Intake/exhaust leak, AIR system, MAFNAF sensor, fuel pressure/pump, injector(s), HO2S
J1939 DTC example:
- Diagnostic Information:
- SPN: 97 FMI: 3 Occurrence Count: 1 Conversion Method: 0
- SPN Name: Water In Fuel Indicator 1
- SPN Description: Signal which indicates the presence of water in the fuel. 00 – No 01 – Yes 10 – Error 11 – Not available
- FMI Fault Code: 428
- Lamp Status: Amber
- Manufacturer: Cummins
- FMI Description: Water in Fuel Sensor Circuit – Voltage Above Normal, or Shorted to High Source
Tips & Best Practices
Groups:
- When creating Maintenance Plans, use Groups to associate your assets to the plan.
- When new assets are created and added to the Group,
they are automatically included in all scheduled maintenance plans for
that Group.
- If practical, use the “Apply to Entire Company” option.
Fixed vs. Variable Service Intervals:
- Fixed service intervals: more commonly used with engine hour-based plans for heavy equipment and machinery. These require service at an exact interval or risk the chance of a breakdown.
- Variable service intervals: more common with light- to medium-duty fleet vehicles, where the distance driven is more important.
Due and Overdue:
- Maintenance can be set to be “Due” at any point between 50%-99% of the interval.
- Once an asset reaches 100% or greater past its
interval, then it is Overdue.
- Example:
- You have a service plan scheduled for every 10,000 miles. You want enough lead time to bring the asset in for service, so you want to know when it is 100 miles away from 10,000 miles (9,900 miles).
- Solution: Set the Due/Overdue Percent to 99%. This will change the status to Due at 9,900 miles (10,000 × 99%). It will be Overdue at 10,000 miles.
Maintenance Costs:
- To keep track of your maintenance costs, you can enter the total Parts and Labor costs for each service that is logged.
- The total cost of all maintenance for an Asset is displayed on the Maintenance Tab on the Asset Dashboard.
- To view the total cost of maintenance for your entire fleet: Export the Maintenance Logs to Excel, and summarize the Total Cost column.
Service Reminders / Maintenance Alerts:
- You can create Service Reminders via “Maintenance Due/Overdue” alerts.
- An alert event will trigger for each asset that becomes Due or Overdue for maintenance. Alert notifications can be sent out as email or SMS text messages with the maintenance plan and service tasks listed for the upcoming service that is due.
- A best practice when creating Alerts is to apply the alert to a specific Group, Groups or Entire Company.
DTC Alerts:
- You can create “Check Engine / Diagnostic (DTC)” alerts which will trigger for each asset that encounters an engine fault.
- DTC Alert notifications can be sent out as email or SMS text messages along with the DTC codes and standard code descriptions.
- A best practice when creating Alerts is to apply the alert to a specific Group, Groups or Entire Company.
Reports:
- The Maintenance Status Report shows the Maintenance Due Status for all assets. It can be run at any time, or scheduled to run daily, weekly, monthly, etc.
- The Check Engine / Diagnostics (DTC) Report is a historical view of all DTC Events, including Trouble Codes and Trouble Code Diagnostic Messages per Asset. The DTC Report can be run on-demand or scheduled.